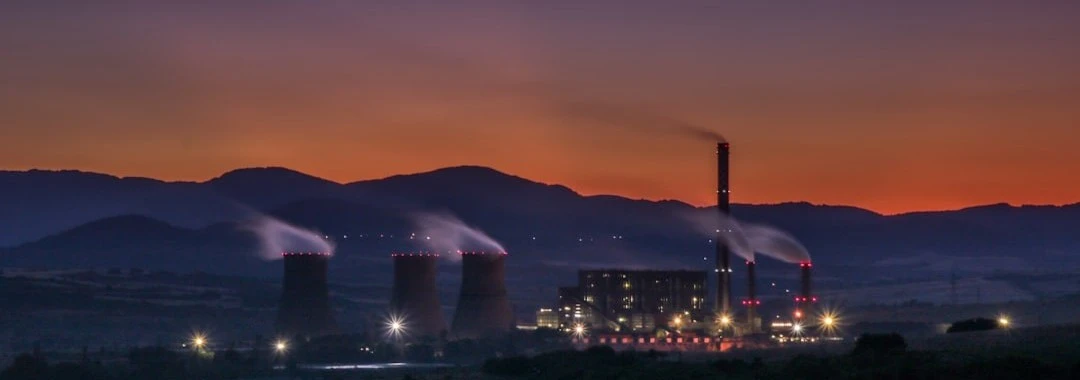
Tanso Carbon / Industrial Applications
Tailored Carbon Capture Applications for Industrial Decarbonization
As an innovative and experienced carbon capture project developer and service provider, we deliver tailored technical solutions to meet the needs of various applications, accelerating our clients' progress toward emission reduction goals.
Multi-scenario Industrial Applications
Our technology offers multi-scenario adaptability, enabling effective performance across diverse industrial applications. From high-emission sectors like cement, steel, and power generation to specialized industries such as biogas upgrading, ammonia production, and shipping, our solutions are tailored for efficient CO₂ capture and effective integration into existing processes.
With scalable, modular designs, our technology adapts to varying conditions and emission profiles. It excels in complex industries like refineries and space-constrained applications such as onboard shipping CCS, helping industries achieve significant CO₂ reductions while optimizing energy use and supporting sustainability goals.
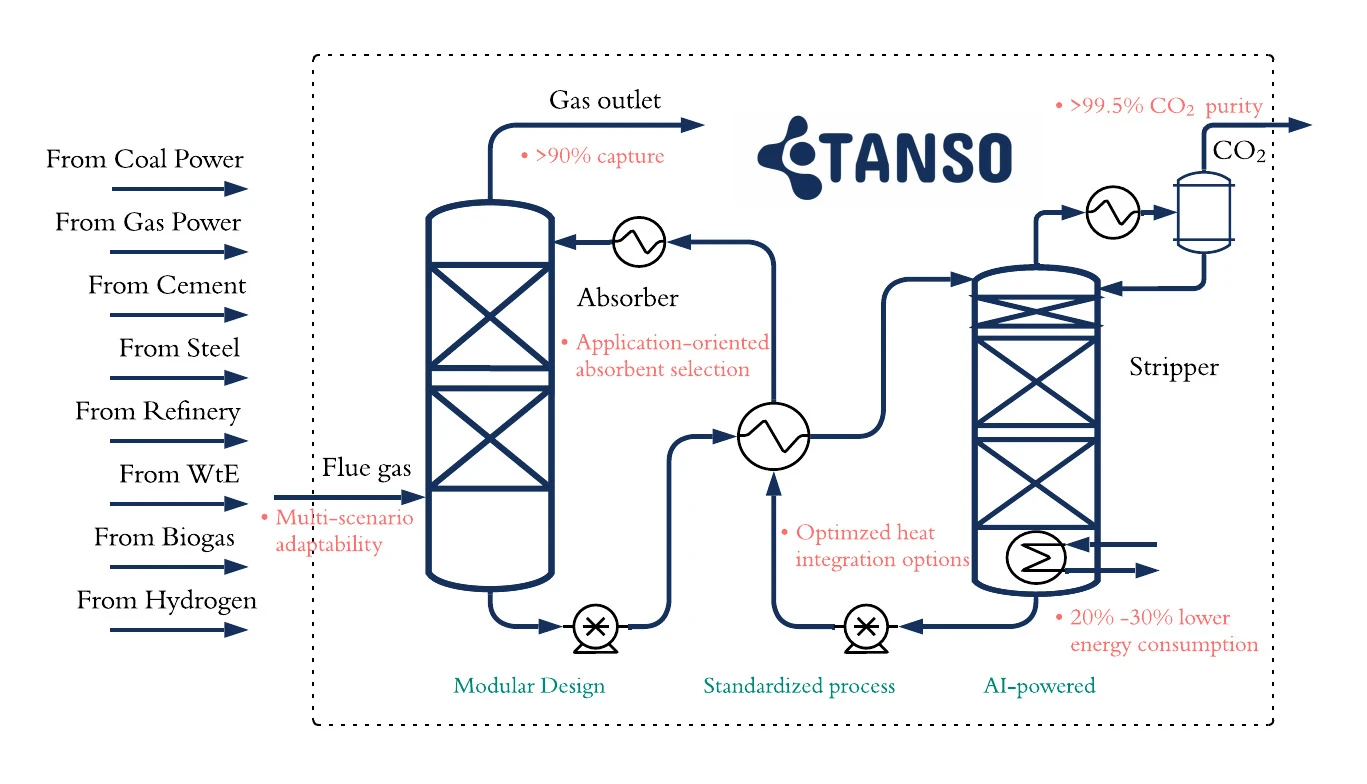
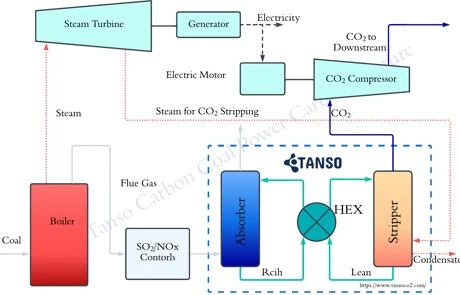
Coal-fired power plant CCUS
Coal-fired power plants are major CO₂ emitters, with challenges including low CO₂ concentration in flue gases, high energy demands for capture, and costly retrofitting requirements. These factors, combined with integration difficulties and uncertain storage solutions, hinder the large-scale adoption of CCUS in these plants.
We provide advanced solvent-based carbon capture solutions designed for coal-fired power plants. Our technology efficiently captures CO₂ while integrating waste heat recovery to reduce energy demands. Modular and cost-effective, our solutions enable effective integration, helping plants achieve significant emission reductions and meet decarbonization goals..
Case study: Development of an amine-based carbon capture process for a coal-fired plant with a flue gas flow rate of 1,130,000 m³/hr, designed to capture 1,000,000 metric tonnes of CO₂ annually.
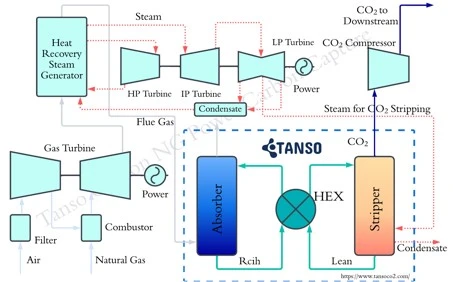
Gas-fired power plant CCUS
Gas-fired power plants face unique CCUS challenges due to low CO₂ concentrations (4-8%) in flue gases, making separation energy-intensive and costly. The high oxygen content also accelerates solvent degradation, raising maintenance costs. Retrofitting these plants requires careful integration to maintain efficiency and compatibility.
Our amine-based carbon capture technology is optimized for gas-fired power plants, capturing CO₂ efficiently from low-concentration flue gases. By using advanced solvents and innovative heat integration process, we minimize energy and operational costs..
Case study: Amine-based carbon capture process development for a gas-fired plant with a flue gas flow rate of 300,000 m³/hr, achieving an annual CO₂ capture of 170,000 metric tonnes.
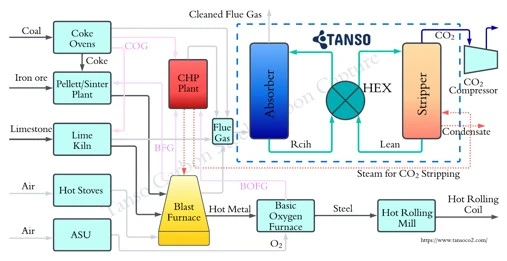
Iron & steel plant CCUS
Steel production contributes 7-9% of global CO₂ emissions, with carbon-intensive processes like BF-BOF steelmaking posing significant decarbonization challenges. The diverse emission sources, high energy demands, and need for extensive customization complicate carbon capture implementation. inconsistent capture rates and high costs further limit its widespread adoption.
Tanso Carbon offers advanced solvent-based carbon capture technology designed for steel plants. Our systems efficiently capture CO₂ from key sources like blast furnace gas, integrating waste heat recovery to reduce energy consumption. Tailored to the unique needs of steel mills, our scalable solutions ensure significant emission reductions.
Case study: Development of a partial carbon capture process for multi-stack flue gas with a flow rate of 480,000 m³/hr, capable of capturing 1,420,000 metric tonnes of CO₂ annually.
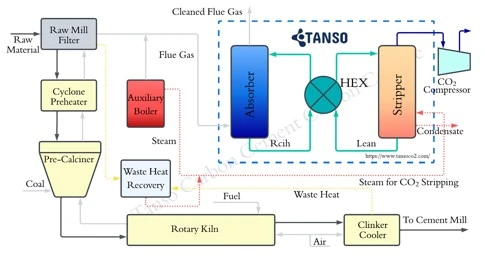
Cement plant CCUS
Cement production contributes approximately 8% of global CO₂ emissions, primarily due to the calcination process that releases significant CO₂. Implementing CCUS in cement plants presents challenges such as high energy consumption, complex integration with existing processes, and economic feasibility concerns.
We offer tailored carbon capture solutions using advanced solvent-based technology to efficiently capture CO₂ in cement production. By integrating waste heat recovery and optimizing energy use, our approach reduces emissions while maintaining efficiency and supporting sustainability goals.
Case study: Development of a carbon capture process for a kiln stack with a flue gas flow rate of 620,000 m³/hr, achieving an annual CO₂ capture of 700,000 metric tonnes.
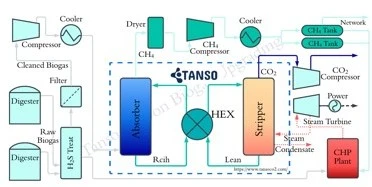
Biogas upgrading plant CCUS
Biogas upgrading plants face challenges in CCUS due to variable gas compositions, impurities like H₂S, high flow variability, and integration complexities with existing upgrading processes. The small scale of biogas plants also makes carbon capture more cost-sensitive compared to larger facilities.
Our technology emphasizes cost-effectiveness by fully utilizing digestate and offering combined removing CO₂ and H₂S. This integrated approach streamlines the upgrading process and enhances overall efficiency, enabling biogas plants to achieve carbon reduction operations with optimized resource utilization.
Case study: TEA study of an ammonia-based carbon capture process for biogas upgrading, capturing 5,500 metric tonnes of CO₂ annually from a 1,000 m³/hr flue gas flow.
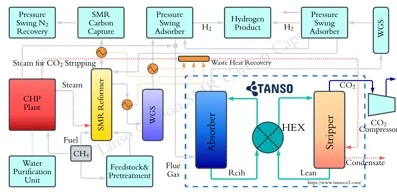
Refinery plant CCUS
Refinery plants face challenges in CCUS implementation due to diverse emission sources, varying CO₂ concentrations, and high energy demands for capture. Retrofitting existing infrastructure is costly and complex, requiring careful integration to avoid production disruptions.
Our tailored CCUS solutions efficiently capture CO₂ from multiple emission points using advanced solvent-based systems. By integrating waste heat recovery, advanced solvent and optimizing energy use, we reduce energy demands and ensure effective integration, helping refineries achieve significant emission reductions and meet decarbonization goals.
Case study: Development of a carbon capture process for two catalytic cracking units with a flue gas flow rate of 460,000 m³/hr, designed to capture 1,300,000 metric tonnes of CO₂ annually.
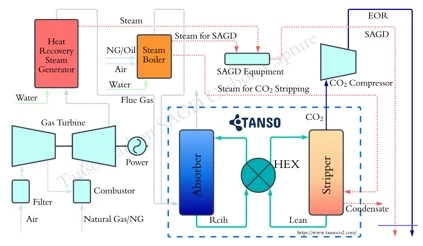
SAGD/EOR CCS
Steam-Assisted Gravity Drainage (SAGD) operation face challenges in CCS due to large CO₂ emissions from boilers and steam generators with variable compositions and high water content, complicating carbon capture. Remote site locations add overall financial and technical hurdles of deployment.
Our novel CCS solutions efficiently capture CO₂ from boilers and and steam generators using advanced post-combustion technologies. By integrating capture-EOR and modular designs, we reduce costs and simplify implementation, supporting SAGD/EOR operators in carbon emission reduction.
Case study: Process development of a SAGD flue gas carbon capture system with a flue gas flow rate of 10,000 m³/hr, achieving an annual CO₂ capture of 9,900 metric tonnes.
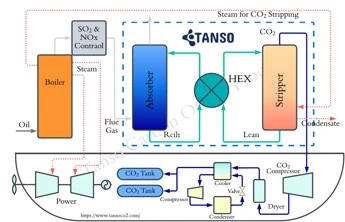
Shipping Onboard CCS
Ship transportation contributes around 3% of global CO₂ emissions. Onboard CCS (OCCS) faces challenges like space constraints, high energy demands, and integrating with ship systems. Flue gas with low CO₂ concentrations, onboard CO₂ storage, and high costs further complicate adoption in the shipping industry.
Our compact CCS systems use advanced solvent-based technologies to efficiently capture CO₂ from ship exhaust, with optimized storage for offloading at ports. Modular and energy-efficient, our solutions reduce emissions and support compliance with decarbonization goals.
Case study: Process modeling of an onboard carbon capture system for a commercial container ship with a flue gas flow rate of 50,000 m³/hr, designed to capture 53,000 metric tonnes of CO₂ annually.
Other Industries We Support

Pulp paper plant CCUS
Tanso capture technology for flue gas from lime kilns and recovery boilers.
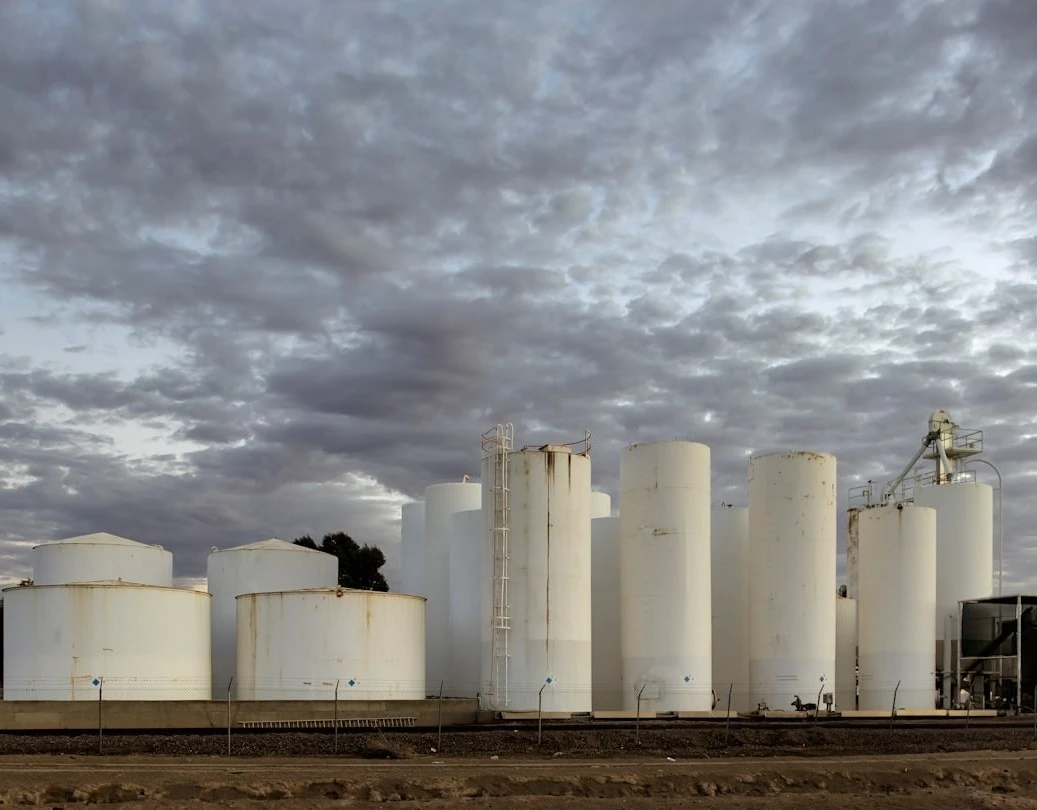
Fertilizer plant CCUS
CO2 capture process for flue gas from primary and secondary reformers.
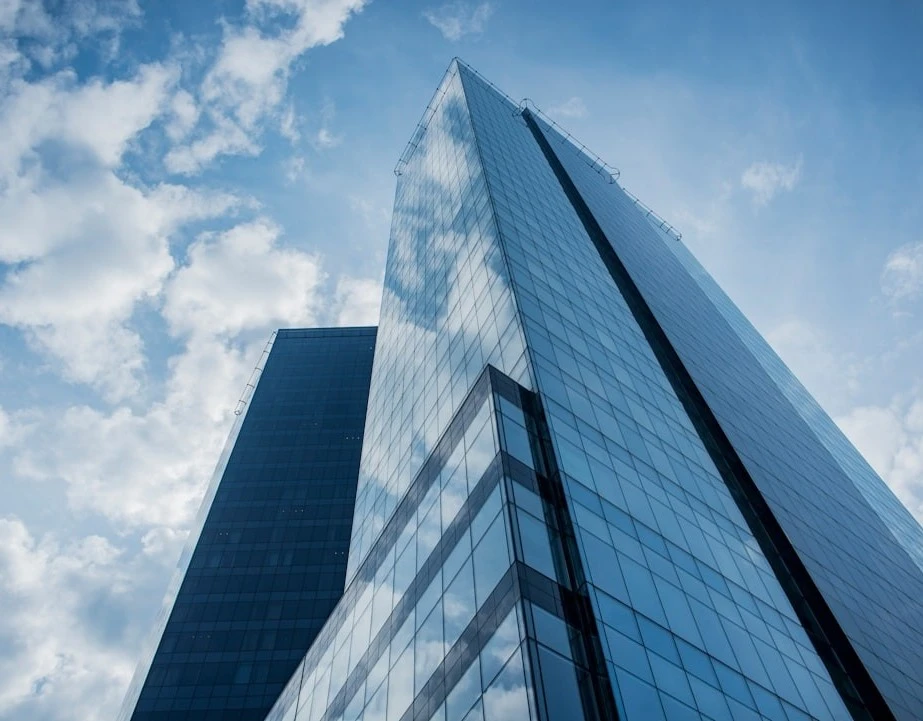
Building carbon capture
Integrating Tanso carbon capture systems into HVAC and ventilation systems.
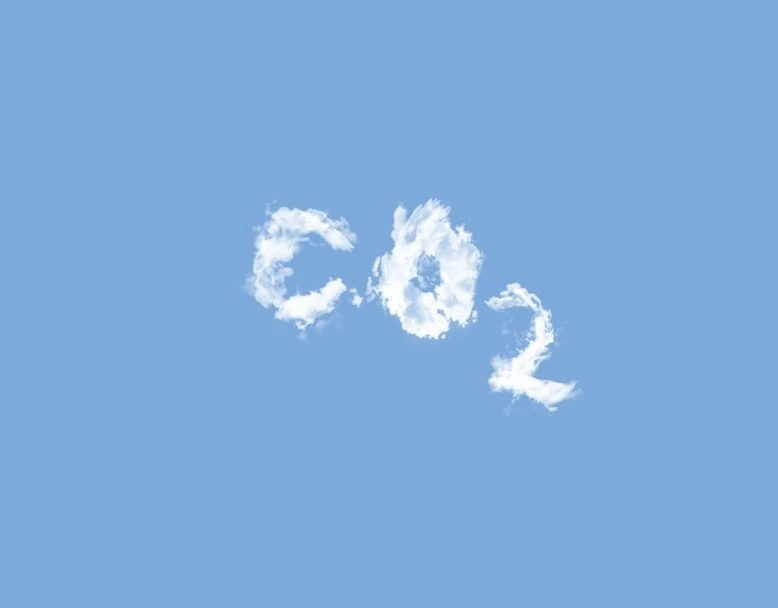
Direct air capture
Extracting CO₂ directly from the atmosphere using Tanso advanced process.